– Sistemas críticos HVAC en la industria farmacéutica – -Calificación De Condiciones Ambientales
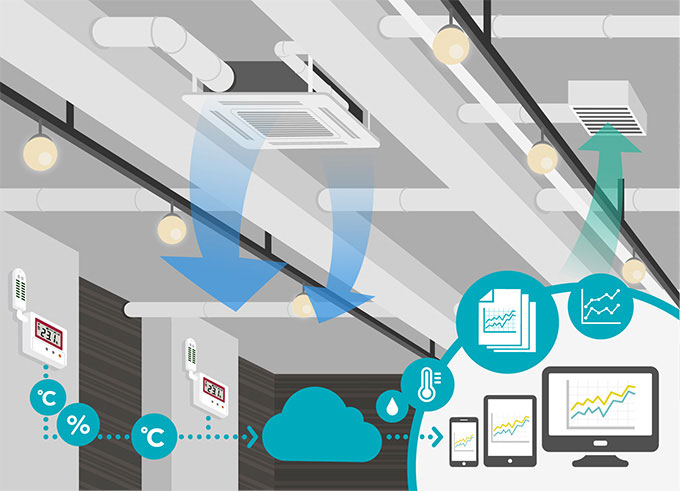
Articulo extraído y ajustado de Mundo HVACR http://www.mundohvacr.com.mx/mundo/2014/02/sistemas-criticos-hvac-en-la-industria-farmaceutica/
Alejandro Jiménez Esquivel
Uno de los sectores de la industria que requiere mayor atención en diseño, cálculos, instalación, definición de especificaciones, precisión, interventoría, control y evaluación estricto y permanente de las condiciones ambientales para los sistemas HVAC, es el sector de la industria farmacéutica.
Equipos de extracción, suministro, colectores de polvo, ductos, prefiltros, filtros, intercambiadores de temperatura, sensores, elementos de control y potencia, difusores, rejillas entre otros elementos de estos sistemas, se eligen mediante la aplicación de estudios de diseño de acuerdo a capacidad requerida, con base en los elementos establecidos por la normatividad aplicable, de acuerdo a la calidad de aire requerida y requerimientos de los procesos en los cuales van a interrelacionar directa o indirectamente, de modo que los procesos sean óptimos, los productos, de calidad, y el personal permanezca seguro y con niveles de confort adecuados.
La industria farmacéutica es uno de los sectores que requiere de los más estrictos controles de aire en el ambiente interior de las áreas de limpias de las plantas de producción. La norma ISO 14644 y las normas BPM de la OMS, establecen los requisitos mínimos que se deben cumplir en los procesos de fabricación de los medicamentos, además de las especificaciones que algunos productos requieren, como condiciones específicas de temperatura, humedad y calidad de aire para ser fabricados.
Los sistemas HVAC dentro de la industria farmacéutica son considerados críticos, al igual que los sistemas de agua purificada, WFI, vapor puro y aire comprimido, debido a que están en contacto directo con el producto.
Cada laboratorio cuenta con métodos definidos, escritos aprobados e implementados para llevar a cabo las llamadas “Buenas Prácticas de Fabricación” (BPF) durante todo el proceso de producción, los cuales suelen superar en ocasiones los requisitos mínimos de la normatividad establecida. De este modo, los sistemas HVAC no están exentos del riguroso monitoreo y de los requisitos obligatorios al momento de llevar a cabo la validación del sistema.
![]() Preliminar. La investigación previa sobre el medicamento por fabricar definirá el tipo de sistema HVAC idóneo a instalar. |
DISEÑO
Decidir cuál sistema HVAC es el correcto al momento de diseñar e instalar depende en gran medida de cómo se clasificarán las áreas de producción, lo cual se realiza con base en el tipo de medicamento que se desea fabricar. Básicamente, existen dos grupos de medicamentos: los estériles y los no estériles. Para cada grupo, la norma ISO 14644 y el informe 32 de la OMS, clasifica las áreas de producción según el grado de asepsia necesario para su fabricación.
Dentro del grupo de los medicamentos estériles, podemos encontrar, entre otros, todos los medicamentos inyectables. En el grupo de los medicamentos no estériles, se hallan, como formas farmacéuticas, tabletas, cápsulas, jarabes, suspensiones, emulsiones, ungüentos, cremas, geles, entre otros.
El grupo de ingenieros encargado del diseño de las instalaciones farmacéuticas y el sistema HVAC deberá realizar un estudio detallado previo, teniendo en cuenta tipo de medicamento que se desea fabricar y la clasificación que le corresponde al área donde se desea realizar la producción, antes de comenzar a desarrollar cálculos o estimaciones; esto ayudará a seleccionar el equipo necesario para integrar el sistema.
En sí, el diseño correcto del sistema HVAC es de suma importancia; primero, porque se debe cumplir con lo especificado en la normatividad vigente; segundo, porque, cuando finalmente los equipos estén instalados, el propio sistema no debe ser fuente de contaminación o generar contaminaciones cruzadas, y tercero, porque dentro de las unidades manejadoras de aire y dentro de los ductos no debe haber crecimiento de hongos, levaduras, bacterias o cualquier otro tipo de contaminación que comprometa la calidad de las áreas limpias, el producto o incida de manera negativa en la salud y la seguridad del personal.
Las contaminaciones cruzadas son de los aspectos más importantes que se desean evitar en la industria farmacéutica. Todos los procedimientos de fabricación, desde la recepción de las materias primas hasta la obtención del producto final, están elaborados para evitar contaminaciones cruzadas; incluso la arquitectura de la planta se diseña para cumplir con el mismo objetivo.
![]() Precisión. Los rangos exactos de temperatura, presión y humedad son vitales para el resultado |
Uno de los cuestionamientos más comunes que surgen al momento de empezar a diseñar el sistema crítico HVAC para las áreas de producción farmacéutica es determinar si se puede retornar o no el aire que es suministrado a las áreas. Por lógica, se sabe que al retornar cierta cantidad de aire se logra un ahorro bastante considerable de energía. Desafortunadamente, los retornos no siempre son permitidos, aunque, si se fabrica dentro de las áreas el mismo producto y no se produce polvo con gran volumen, es posible retornarlo. No obstante, si los productos fabricados son diversos o se produce gran cantidad de polvo, lo conveniente es extraer el aire con otro equipo independiente al de inyección y descargarlo hacia la atmósfera, no sin antes filtrarlo para eliminar cualquier contaminante tóxico para el medioambiente.
La norma ISO 14644, se enlistan cinco clasificaciones que, de acuerdo con el proceso de fabricación, definen las características que deben cumplirse, como el número máximo de partículas totales por cada metro cúbico de aire, el número máximo de partículas viables (UFC, unidades formadoras de colonias) permitido, tanto en condiciones dinámicas como en condiciones estáticas, con un tamaño de partícula que pueden estar entre 0.5 y 5.0 μm, igual que la frecuencia de monitoreo ( 0.1, 0.2, 0.3, 0.5, 5,0 y 10.0 μm son los tamaños de partícula que pueden ser evaluados, de los cuales tomaremos mínimo dos (2) tamaños de partícula diferente, teniendo en cuenta que la diferencia entre los dos tamaños de partícula seleccionadas debe ser mayor a 2.5 diámetros).
Se definen también las presiones diferenciales mínimas que deben existir entre áreas, ya sea de la misma clasificación o diferente, y el sentido de flujo que debe tener el aire. Armonizado y unido a esto, se definen los cambios mínimos de aire por hora y los rangos de temperatura y humedad relativa dentro de las áreas, así como la vestimenta necesaria de ingreso.
El sistema HVAC deberá estar diseñado para cumplir con estos requisitos. Si bien son bastante exigentes, no son imposibles. Lo importante es entender correctamente los requisitos para cada clasificación.
NOTAS:
a) Los ejemplos aquí señalados son enunciativos, no limitativos.
b) Placa de sedimentación de 90 mm de diámetro, con exposición no menor a 30 minutos y no mayor a 4 horas o al tiempo validado, durante todo el tiempo que dure la operación.
c) Muestreo microbiológico de 5 dedos de los guantes.
d) La zona de flujo laminar debe cumplir con un parámetro de velocidad de flujo 0.45 m/s ± 20%.
e) Puede realizarse con mayor frecuencia de acuerdo con el mantenimiento del estado validado.
f) Podrá ser realizado al menos en ISO-Clase 8, siempre y cuando se soporten con estudios de validación.
g) Los cuartos clasificación ISO-Clase 5 deben cumplir con estos parámetros.
Filtración
Una característica muy significativa de los sistemas HVAC dentro de la industria farmacéutica es el filtrado, tanto del aire que ingresa a las áreas, como de las extracciones y colección de polvos. El tipo de filtro, su eficiencia o si es terminal, es decir, colocado a nivel de plafón.
El sistema HVAC debe estar diseñado e integrado de forma tal que permita cumplir con la clasificación del área requerida. Los correspondientes a clase ISO 5, 6 y 7 deben contar, como mínimo, con filtros terminales HEPA de 99.97% de 0.3 μm. En el caso de clase ISO-8, deben contar, como mínimo, con filtros de eficiencia de 95% y para clase ISO-9 deben contar, como mínimo, con filtros de eficiencia de 85%
Los filtros terminales para las clases ISO 5, 6 y 7, además de la eficiencia ya definida, deben contar con un gabinete hermético, y los accesorios deberán estar instalados de manera que faciliten las pruebas de integridad que se realizan a los filtros periódicamente por el departamento de validación. Es conveniente que el filtro tenga en su perímetro un sello de gel, silicona u otro sellante adecuado para lograr hermeticidad entre el filtro y el gabinete; con esto se proporcionará un conteo de partículas optimo o aceptable.
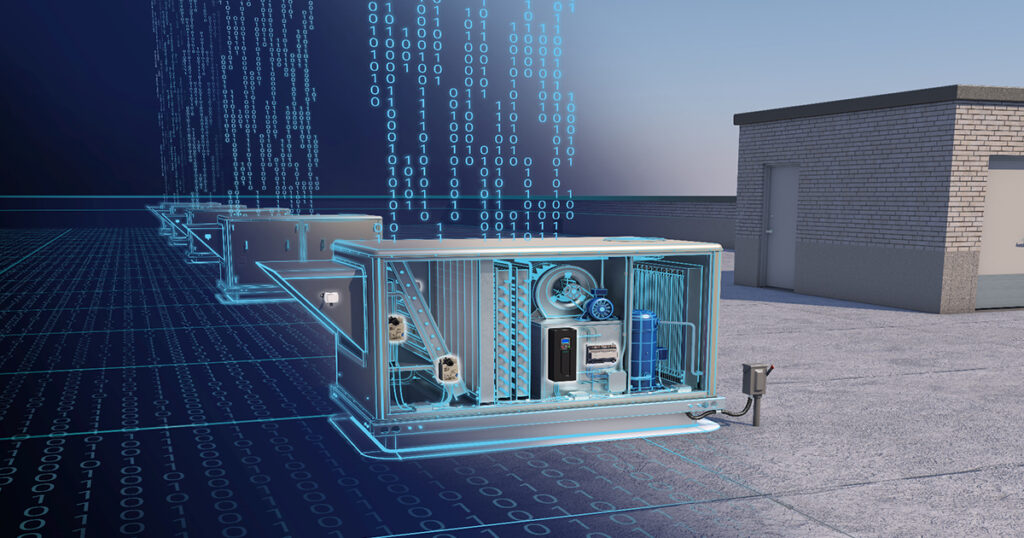
Las pruebas de integridad que se realizan a los filtros terminales HEPA, con 99.97 por ciento de eficiencia, son hechas para garantizar que los filtros no se encuentren rotos o con defectos de fabricación. Como el conteo de partículas en la clase ISO-5 es un parámetro de liberación o de continuo monitoreo durante el proceso de llenado aplicado para los medicamentos inyectables, es de suma importancia garantizar que los filtros atrapen las partículas contaminantes en su superficie.
Dentro de los componentes del sistema HVAC, como las manejadoras de aire, también se deben colocar filtros de aire por etapas; comúnmente son tres. Una manejadora de aire que dará servicio a un área de producción ISO-Clase 8 para medicamentos no estériles llevará en la primer etapa filtros plisados de 35 por ciento de eficiencia; esto, para evitar la acumulación de polvo dentro de la unidad y para servir como protector de la siguiente etapa de filtrado. En la segunda etapa de filtrado se suelen colocar filtros con 65 a 70 por ciento de eficiencia como pre-filtros, que ayudarán a la protección de la tercera etapa, la cual finalmente dará la eficiencia de 95 por ciento que exige la norma.
En ocasiones, algunos laboratorios exigen que se les instalen filtros HEPA de 99.97 por ciento de eficiencia en la tercer etapa, en lugar de uno de 95 por ciento; esto, con el fin de garantizar un conteo de partículas mucho menor que el mínimo que especifica la norma; por tanto, el filtro de 95 por ciento se coloca en la segunda etapa. Esto también es permitido por las autoridades.
En las extracciones se debe cuidar que el aire descargado a la atmósfera no contenga residuos de medicamento. Para esto, el aire debe filtrarse con una eficiencia similar a la de inyección para evitar, como ya se mencionó, el paso de contaminantes al medioambiente.
Es preciso recordar que existe una cantidad muy variada de medicamentos que pueden ser tóxicos, como los hormonales, los cuales pueden causar efectos considerables en el cuerpo humano si se somete a exposición prolongada. Es importante mencionar que se deben monitorear constantemente los ductos de descarga de las extracciones y de los colectores de polvo mediante puertos de muestreo de fácil acceso.
Los filtros deben cambiarse de acuerdo con un programa validado de mantenimiento. Debe existir un procedimiento normalizado de operación PNO que defina cómo y cuándo debe de llevarse a cabo. La norma ISO 14644 pide que se tengan instalados manómetros de presión diferencial en todos los equipos que contengan filtros, cuya lectura deberá ser registrada máximo semanalmente para evitar que los filtros colapsen en caso de encontrarse demasiado saturados. Los filtros sucios no deben tirarse a la basura; deben ser retirados con cuidado, sin sacudirlos, para finalmente llevarlos a confinamiento y definir su disposición final con una empresa autorizada para realizar esta labor.
Cambios de aire
El cálculo de la cantidad de aire por suministrar se debe realizar respetando los cambios de aire por hora que especifica la norma. También se recomienda realizar un cálculo de cargas térmicas sensibles y latentes, tanto interiores como exteriores, en verano y en la época de invierno; considerar la cantidad de personas que labora por turno, la cantidad de motores pertenecientes a los equipos de producción, la incidencia de la radiación solar en las paredes exteriores (cuando aplique) y el calor generado por el producto cuando se fabrique a altas temperaturas.
De los dos resultados obtenidos, ya sea por cambios o por cargas térmicas, se debe de tomar siempre el mayor; de lo contrario, se correría el riesgo de cumplir con los cambios establecidos, pero quedar cortos en la capacidad de enfriamiento o calefacción de los equipos, y que éstos nunca brinden la temperatura deseada.
![]() Hermeticidad. Cuanto mejor sea el sello de las puertas, mayor será la presión diferencial y menores los cambios de aire por hora |
Sentidos de flujo
Los sentidos del flujo de aire de las infiltraciones por las puertas se definen al considerar si el área es negativa o positiva, de acuerdo con su clasificación, o si dentro de las áreas se genera demasiado polvo, como en las áreas de pesado, compresión y mezclado.
Las puertas utilizadas dentro de la industria farmacéutica tienen un sello perimetral que permite mantener una presión fija, siempre y cuando se mantengan cerradas. Si se conoce la cantidad de aire por suministrar y la cantidad de aire de infiltración que entra o sale por las puertas, es posible calcular el caudal de aire de retorno o de extracción, según sea el caso. Por ejemplo, si se desea saber la cantidad de aire por suministrar a un cuarto en particular y también se quiere conocer la cantidad de aire que se podrá retornar, lo primero que se necesita saber es el volumen del cuarto en cuestión. Entonces, si se tiene un valor de 30 metros cúbicos, lo siguiente es multiplicarlo por los cambios de aire por hora que define la norma, de acuerdo con la clasificación; para fines de este ejemplo, se utilizarán como mínimo 10 cambios por hora. El resultado de estos datos sería de 300 m³/h, que indica el caudal de aire por suministrar al área para cumplir con los cambios. Ahora, si además se tiene una infiltración de aire de 100 m³/h por las rendijas de las puertas, el resultado sería de 400 m³/h de aire total suministrado. En resumen, la cantidad de aire que será suministrada por el difusor de inyección será de 300 m³/h y la cantidad de aire que retornara al ambiente a través de las rejillas de retorno será de 400 m³/h; así, se cumple el balance de materia o flujo volumétrico.
Por otro lado, si se tuviera no sólo un cuarto, sino diez, se tendrían que desarrollar los cálculos para cada uno de ellos y finalmente sumar la cantidad de aire total, que indicará la cantidad de aire que tendría que mover la unidad manejadora o el equipo de extracción. El caudal de aire de las infiltraciones se calcula con base en el área de paso del aire por las rendijas de las puertas, respecto de una velocidad de paso.
Presiones diferenciales
Según la Norma ISO 14644, a cada clasificación corresponde una presión diferencial; cuanto mejor sea el sello de las puertas, mayor será la presión diferencial. En caso de que las puertas no sean de grado farmacéutico, la falta del sello se puede compensar con el aumento de los cambios de aire por hora; esto elevará la presión diferencial respecto del área adyacente; sin embargo, si existe una presión muy elevada, costará trabajo abrir o mantener cerradas las puertas.
Para saber si se está cumpliendo con las presiones diferenciales mínimas correspondientes, se deben ubicar tableros dentro de las áreas donde sea posible colocar manómetros de presión diferencial para cada puerta por cada área. Las lecturas deben tomarse diariamente para descartar algún problema relacionado con el desempeño del sistema HVAC.
![]() ![]() Periodicidad. Las lecturas de presión diferencial deben tomarse a diario para descartar problemas de desempeño |
Control de temperatura y humedad
El control de temperatura se logra al forzar el paso del aire por medio de serpentines de enfriamiento, ya sean de expansión directa (de gas refrigerante) o mediante un sistema hidrónico de agua helada o caliente.
Si bien la norma pide mantener un rango de temperatura de 18 a 25 grados centígrados para todas las clasificaciones, no quiere decir que se deba mantener una temperatura constante entre 18 y 25 grados centígrados, a menos que las condiciones de fabricación del producto así lo requieran. Es posible entonces mantener una temperatura de, por ejemplo, 22 °C, ± 2 grados, para evitar un consumo excesivo de energía y favorecer las condiciones de trabajo para los operarios de producción.
En el caso de los almacenes, ya sean de materia prima o de producto terminado, las condiciones de temperatura deben garantizar la adecuada calidad del producto. La mayoría de los medicamentos e insumos indican en sus etiquetas que deben almacenarse en un lugar seco y fresco a menos de 30 grados centígrados. Dentro de los almacenes debe comprobarse que, durante el tiempo que el medicamento está en almacenamiento, el aire interior nunca sobrepase los 30 grados.
Las áreas de almacenamiento deben ser diseñadas y construidas para asegurar las buenas prácticas de almacenamiento; deben cumplir con las condiciones de limpieza, temperatura y humedad relativa requeridas por el tipo de insumos o productos, y llevar a cabo su control, monitoreo y verificación.
El control de la humedad relativa es más complejo, pues existen diferentes factores internos y externos que hacen que su condición cambie a través del tiempo. A pesar de que el rango varía entre 30 y 65 por ciento normalmente, lo que parece bastante amplio, el simple hecho de que en el exterior esté lloviendo modifica considerablemente las condiciones interiores si es que el aire de renovación proveniente del exterior es significativo. Existen en el mercado equipos deshumidificadores o humidificadores con vapor, los cuales pueden ser instalados para lograr controlar esta variable. Los equipos más usados para deshumidificar el aire que ingresa en las áreas son los de rueda desecante, a base de sílica gel, donde la regeneración se realiza con aire caliente.
La temperatura y la humedad relativa deben monitorearse y documentarse constantemente antes de la fabricación de un lote y durante el proceso de fabricación.
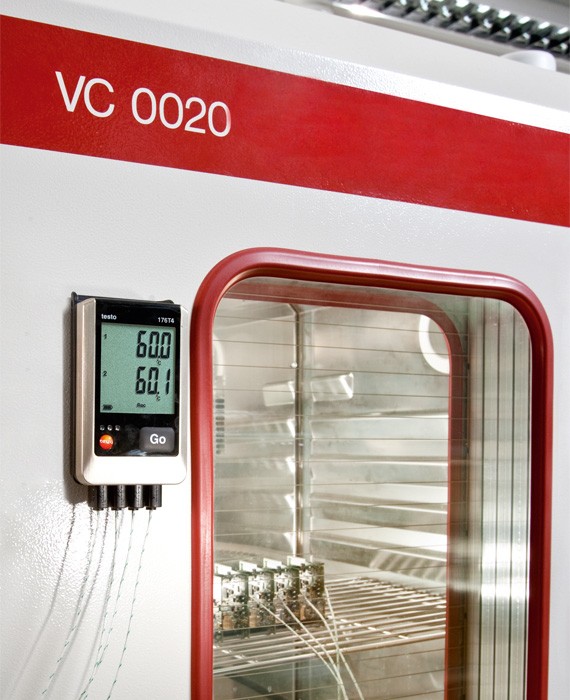
Equipos
• Unidad manejadora de aire
Aunque existen diferentes fabricantes de unidades manejadoras de aire, es importante que la unidad que se instale sea de grado farmacéutico, debido a las características que presentan; por ejemplo, es recomendable que los módulos sean de perfiles de aluminio extraído de 2 pulgadas, unidos mediante esquineros de aluminio fundido. También deben emplearse paneles de doble pared, lámina de acero galvanizado, de aluminio o acero inoxidable, con 2 pulgadas de espesor, recubiertas totalmente con pintura para intemperie si se colocaran en el exterior. Cada módulo cuenta con superficies interiores totalmente lisas para facilitar las tareas de limpieza y mantenimiento, y evitar el crecimiento microbiológico. Las puertas son de construcción, igual que los paneles, con sello hermético y en una sola pieza. Las ventanas de inspección deben estar construidas en policarbonato doble, con un sistema de fijación interior. Las bisagras y cerraduras deberán estar construidas con materiales que eviten puentes térmicos, con manómetros de presión diferencial en cada sección de filtros. En suma, la unidad debe ser capaz de soportar una presión de entre 6 y 8 pulgadas columna de agua para garantizar que cumpla con el límite de fuga permitido.
• Unidades de extracción y colectores de polvos
Las unidades de extracción tienen una fabricación similar a la de las unidades de suministro de aire, sólo que aquéllas cuentan únicamente con el ventilador centrífugo de extracción y la sección de filtros. Los filtros en estas unidades deben ubicarse antes del ventilador de extracción para evitar incrustaciones de medicamento en el motor o en el mismo ventilador.
Los colectores de polvo cumplen la función específica de aspirar el polvo que se genera durante la fabricación de un medicamento; sin embargo, al ser parte de un sistema HVAC, tiene que cumplir con las características de un equipo grado farmacéutico.
Las áreas de producción en las que se generen polvos (muestreo, pesado, mezclado u otro proceso) deben contar con sistemas de extracción y colección de polvos que, por su diseño, eviten contaminación cruzada y al medioambiente.
Lo primero que se debe conocer antes de realizar el diseño de un sistema de colección de polvo para la industria farmacéutica son las características del polvo generado durante la producción; por ejemplo, el tamaño y la densidad de las partículas de polvo, si es higroscópico o tóxico, como los hormonales o penicilínicos, a los cuales algunas personas son alérgicas; en tal caso, el sistema deberá contar con un método de cambio seguro (bag-in bag-out) de filtros ubicados en el colector de polvos o puede utilizar un principio activo altamente explosivo.
• Ductos
Los ductos de inyección, retorno o extracción son construidos comúnmente de lámina galvanizada del calibre correspondiente a las dimensiones del ducto, excepto en aquellos sistemas donde se especifica otro tipo de material. Sólo los ductos expuestos dentro de las áreas de fabricación serán de acero inoxidable.
Algunos laboratorios farmacéuticos suelen preferir los ductos de tipo bridado TDC (Transverse Duct Connections) por los siguientes motivos:
1. Ahorro económico: al ser de mayor rigidez, permite usar calibres de lámina más delgados
2. Ahorro de energía: debido al uso de empaques entre bridas,
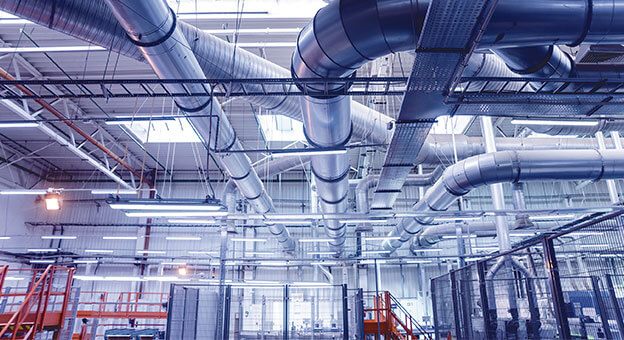
El cálculo de ductos bridados permite el uso de calibres menores gracias a la rigidez obtenida con las bridas tipo TDC; según estudios realizados, el ahorro de material es aproximadamente de 30 por ciento. Por ejemplo, con un sistema de 2 pulgadas columna de agua de presión, en un ducto de 38 pulgadas x 20 pulgadas y 4 pies de largo, si se usa grapa-zeta, se requiere un calibre 22, equivalente a 23.2 kilogramos de lámina; por otro lado, si se usa ducto bridado tipo TDC, se requiere calibre 24, equivalente a 16.5 kilogramos de lámina.
El diseño de estos ductos permite su rápida conexión, sin generar ruido por martilleo. La rigidez del ducto tipo TDC también permite ampliar la distancia entre soportes. El rápido sistema de conexión de los tramos de ducto sólo requiere de 8 tornillos y clips, además de facilitar las labores de mantenimiento y limpieza. Estos ahorros son importantes porque los equipos especializados de grado farmacéutico suelen tener un precio mayor que los de tipo comercial.
En todas las uniones de los ductos debe aplicarse un sello resistente a las condiciones ambientales y, sobre todo, que evite el crecimiento de hongos, levaduras o bacterias. Una vez instalados los ductos, se deben realizar pruebas de hermeticidad, con el fin de garantizar que exista sólo un mínimo de fuga permitido, de acuerdo con la presión de diseño.
Distribución del aire
La distribución del aire se realiza por medio de difusores colocados en el techo, mientras que el retorno de aire o la extracción se realiza con rejillas ubicadas a 30 centímetros sobre el nivel del piso. El objetivo de esto es lograr un barrido del área de producción con el aire de suministro, atrapar las partículas suspendidas y dirigirlas hacia las rejillas para que, finalmente, sean apresadas por el filtro del equipo.
Una característica importante de estos accesorios es que deben colocarse a ras del techo o pared, evitando bordes en los marcos de sujeción donde se pueda acumular el polvo. Los materiales pueden ser aluminio si se instalan en almacenes; en el caso de las áreas críticas o asépticas, los difusores y rejillas pueden ser de acero inoxidable para que se puedan limpiar periódicamente con sanitizante.
Balanceo de aire del sistema HVAC
Todos los sistemas HVAC en la industria deben balancearse por medio de compuertas para garantizar que la cantidad requerida de aire pase por los difusores o las rejillas de retorno. No obstante, en la industria farmacéutica este procedimiento es muy importante, ya que no sólo se obtienen los caudales necesarios, sino que de un buen balanceo de aire se obtienen las presiones diferenciales y los sentidos de flujo de aire que evitarán contaminaciones cruzadas, como lo exige la norma.
Control y automatización
Aunque no se menciona un tipo de control específico del sistema crítico HVAC, sí es claro que se deben mantener y monitorear las condiciones de temperatura y humedad, así como las presiones diferenciales y los sentidos de flujo de aire en las áreas de producción. El control de dichas condiciones se puede realizar de manera sencilla o, si se desea, es posible utilizar un control central que mantenga balanceado el sistema cuando se dejen abiertas las puertas durante tiempos prolongados y las presiones diferenciales no se recuperen durante los 20 segundos siguientes; si esto ocurriera y el sistema no lograra compensar las pérdidas de presión, se emitiría una alarma audiovisual para corregir el problema en la medida de lo posible.
Instalar variadores de frecuencia en los motores de los equipos facilita el balanceo del sistema de aire y también mantiene un flujo constante, aun cuando los filtros de aire se saturen.
Validación
La validación es un elemento esencial para el cumplimiento de las BPF, que permite demostrar la funcionalidad del sistema HVAC. Se trata de un conjunto de calificaciones realizadas por especialistas en el sector. Se define como calificación a la realización de las pruebas específicas basadas en conocimiento científico para demostrar que los equipos, sistemas críticos, instalaciones, personal y proveedores cumplen con los requerimientos previamente establecidos, y debe ser concluida antes de validar los procesos.
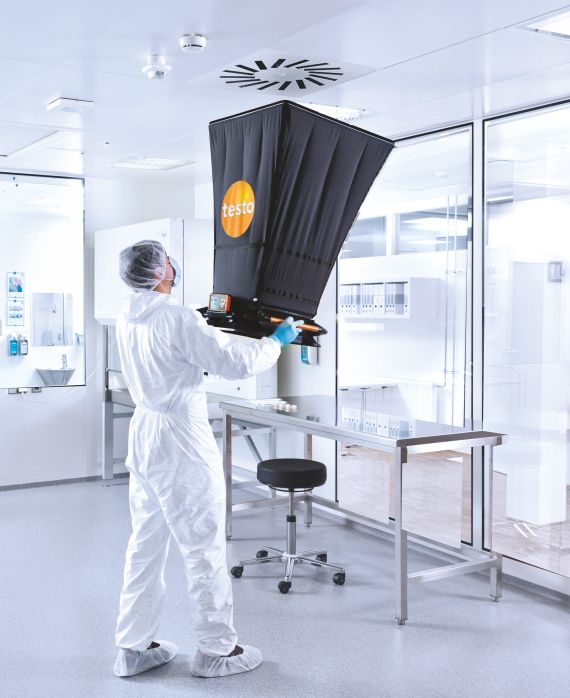
• Evaluaciones recomendadas
De diseño. Es la evidencia documentada que demuestra que el diseño propuesto para las instalaciones, sistemas y equipos es conveniente para el propósito proyectado.
De instalación. Es la evidencia documentada de que las instalaciones, sistemas y equipos se han instalado de acuerdo con las especificaciones de diseño detallado previamente establecidas.
De operación. Es la evidencia documentada que demuestra que el equipo, las instalaciones y los sistemas operan consistentemente, de acuerdo con las especificaciones de diseño funcional establecidas.
De desempeño. Es la evidencia documentada de que las instalaciones, sistemas, y equipos se desempeñan cumpliendo los criterios de aceptación previamente establecidos según USR.
En sí, el diseño, la operación y el mantenimiento de un sistema crítico HVAC para el sector farmacéutico es un reto, pues debe estar en constante monitoreo y validación para que permita continuar con las labores ahí desempeñadas.
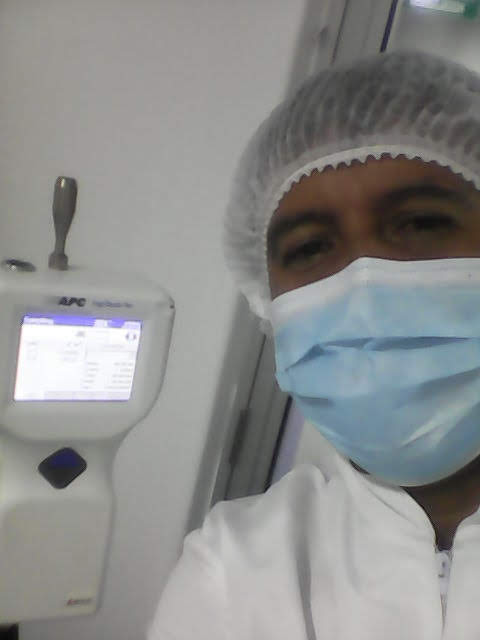